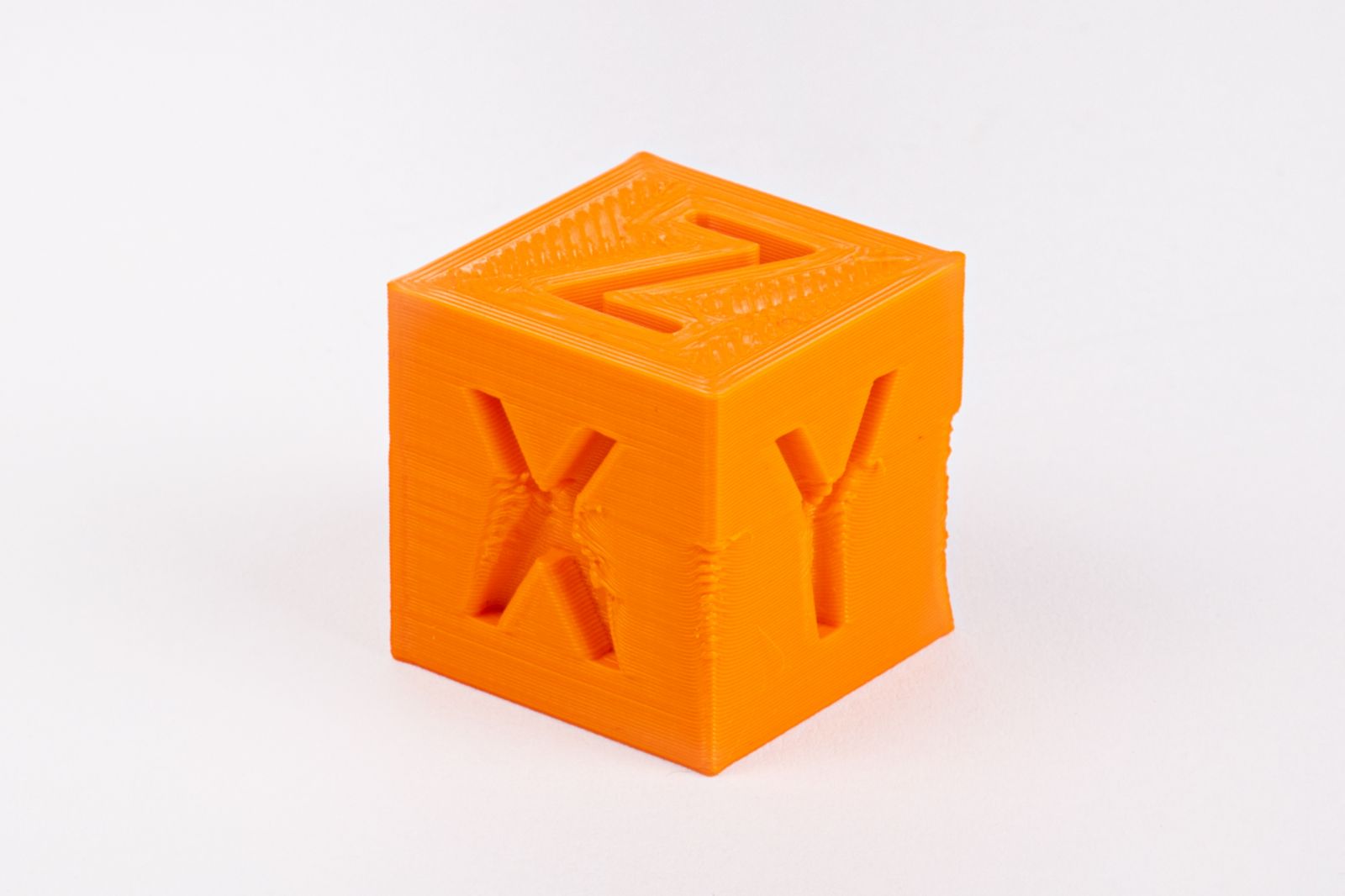 |
The 3D print is out of proportion
Your 3D print is out of proportion when the shape and dimensions deviate from your design. In addition, your design may look 'slumped', as if the structure has collapsed under the weight of the material or any heat from the outside. |
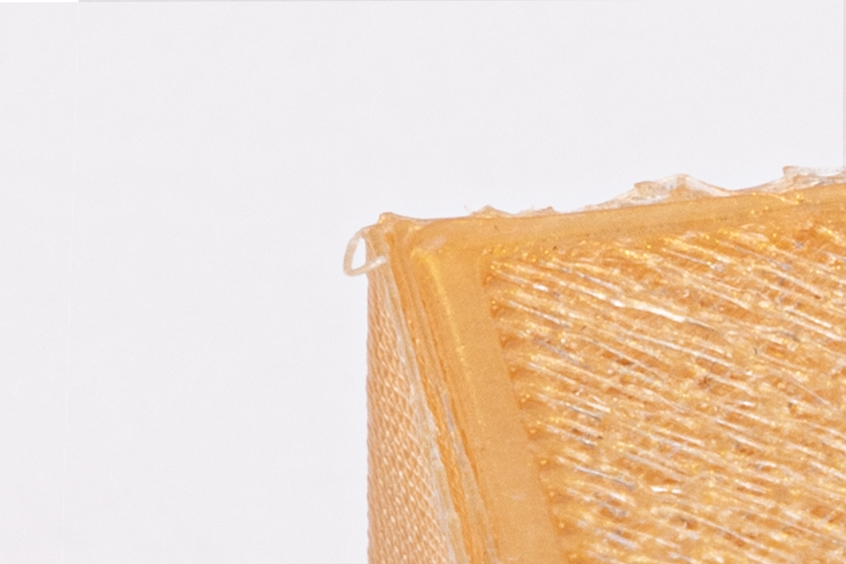 |
The print lines are thick and bumpy
Normally the print lines of your 3D print should be tight and almost invisible. Test this by printing a cube with at least 3 outlines. Does it look like too many layers have been printed or are there drips on the side of the model? Then you suffer from over-extrusion. |
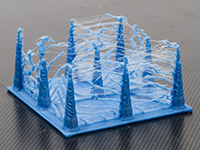 |
The 3D print appears to be shrouded in a kind of 'spider web'
If too much filament is used during printing, the nozzle will leak, causing 'stringing' or 'oozing'. This creates thin wires between the different parts of your print. |